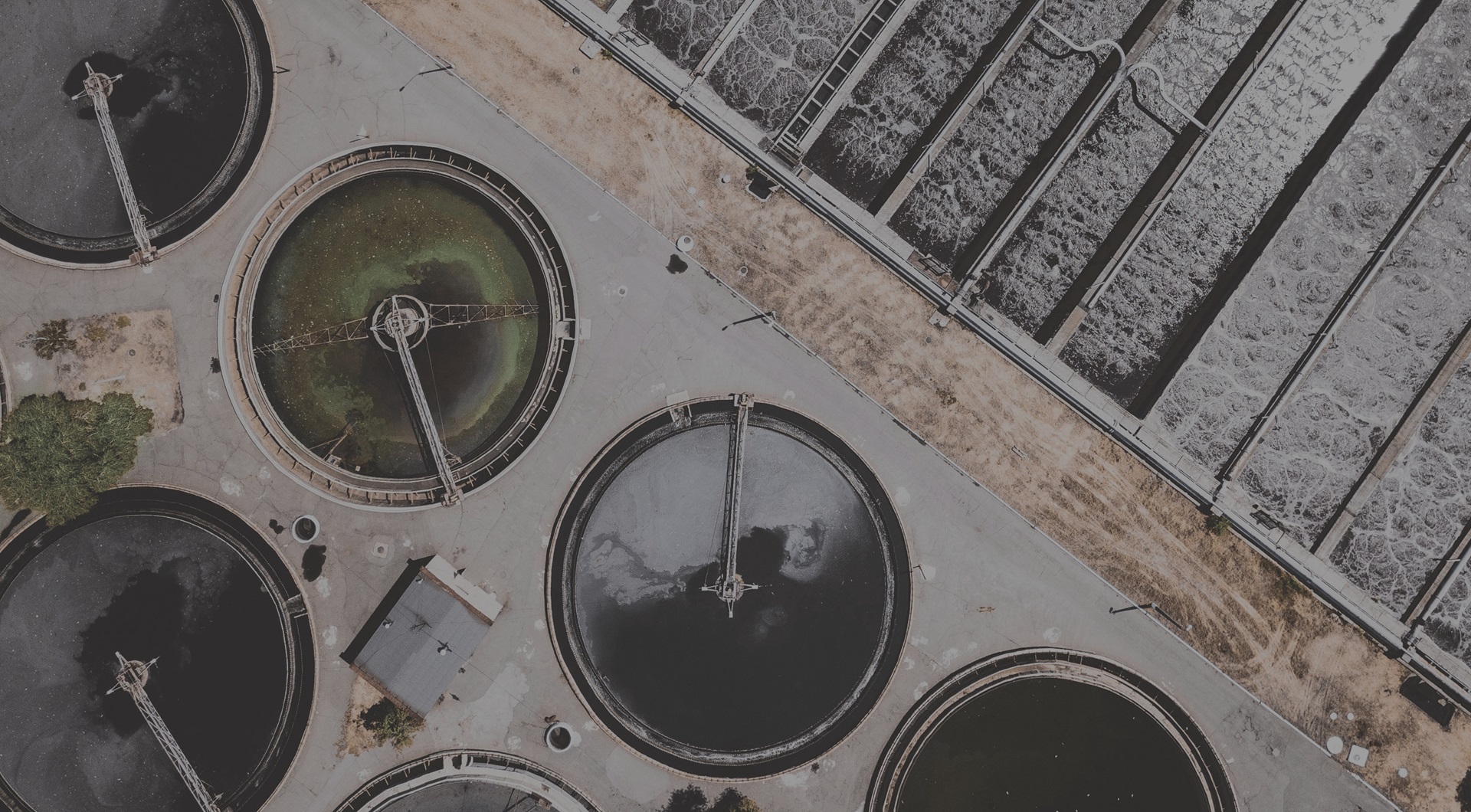
Unique Penstock Challenge under Confined Space Working Conditions for High-profile Project.
Complex and challenging penstock design, manufacture and installation to control wastewater flows through aeration equipment in a high-profile treatment plant prior to discharge into the River Thames.
Skills required included the design and manufacture of an entirely unique penstock, servicing, repair and upgrade of existing penstock assets, and careful planning to optimise time on site which was complicated by the need for both low effluent levels and low tides, all under confined space working conditions.
The challenge
Originally constructed between 1931 and 1936 and subsequently expanded and upgraded on several occasions, Mogden Sewage Treatment Works (STW), located in West London, is the second largest STW in the United Kingdom. It covers an area of 55ha (135 acres), can treat around 1.5 billion litres of sewage and wastewater per day, and services a population of almost 2 million.
Thames Water and the Environment Agency are working to increase the levels of dissolved oxygen (DO) in the upper tideway of the River Thames. The project is referred to as the Lower Thames Abstraction Mitigation Scheme. The presence of a sufficient concentration of dissolved oxygen is critical to maintaining the aquatic life and aesthetic quality of the river and its tributaries.
Fundamental to the success of the scheme was the work at Mogden STW: Mogden STW Final Effluent Oxygenation. This required the aeration of the final effluent from Mogden STW. The new aeration facility is within the main final effluent culvert within the boundary of the site. Controlling the flows passing through this aeration equipment is critical and was achieved using penstocks, designed, manufactured, installed and commissioned by Glenfield Invicta Ltd.
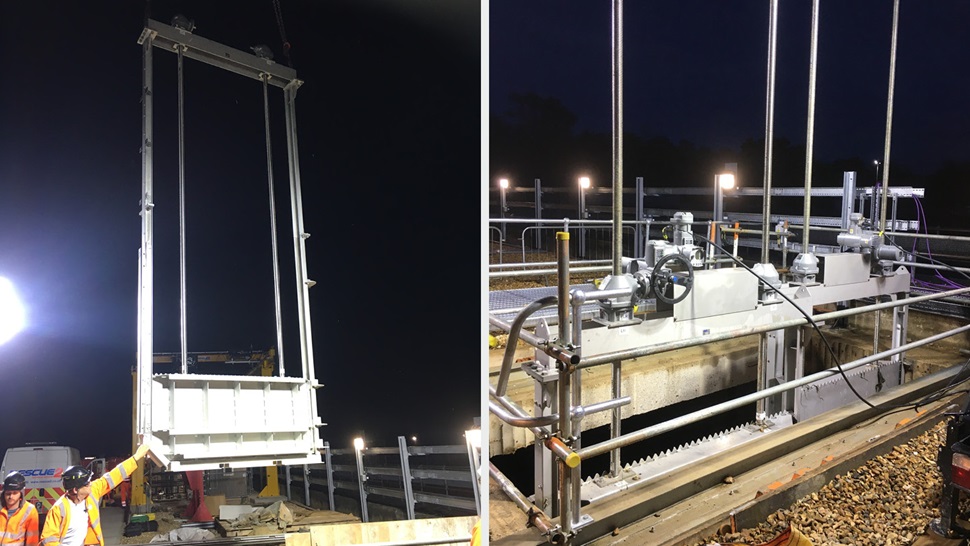
Glenfield Invicta’s scope of works encompassed four main elements:
1 - Design, manufacture, installation and commissioning of the Main Final Effluent Culvert (MFEC) penstock.
The purpose of the MFEC penstock is to maintain a minimum water level (1.5m) to enable the aeration equipment to operate within its process guarantee parameters. The penstocks will only be lowered for the estimated three months of the year when aeration is required and at all other times the gates are to be fully open.
The design of the MFEC penstock consisted of two separate gates in a single frame that is face mounted within the 4.6m wide x 4.7m deep culvert. The gates have their own individual actuator, twin spindles and gearboxes, enabling each gate to operate entirely independently of the other. Consequently, if one gate fails or jams, the other continues to operate.
Each gate is equipped with its own Uninterruptible Power Supply (UPS) to ensure it is able to operate in the event of a mains power failure. The design has several novel features, including passive openings on the frame’s invert member to encourage scouring of the culvert floor, a 4m stroke to lift the gate clear of the maximum top water level and nappe splitters on top of the gates, to reduce vibration and cavitation.
Prior to manufacture, the design of the frame, gates and anchorage was subject to detailed Finite Element Analysis (FEA), independently verified by a third-party testing house, then submitted to the client for approval.
The penstocks were fabricated from stainless steel. This choice of material enabled Glenfield Invicta to create a highly bespoke penstock design that met the customer’s exacting requirements and the precise channel dimensions, but could also be manufactured within a tight eight-week timescale.
Before installation work could proceed, the penstock was subjected to a Factory Acceptance Test (FAT) under the supervision of CABV JV.
Installation of the MFEC penstock was carried out by Glenfield Invicta’s in-house installation team. The work took place at night during seven 4-hour windows. The windows were determined by congruent low effluent flow levels and low tides. The MFEC measured 4.6m wide by 4.7m deep and was only accessible using confined space techniques including winching. A dedicated safety and rescue team was on hand at all times.
Urgent minor adjustments to the penstock were completed at Glenfield Invicta’s Maidstone workshop when it was discovered that civil engineering details provided on record drawings were slightly different to those encountered upon entry to the culvert.
2 - Design and manufacture of a stopgate to provide a secondary means of isolation for the works in the MFEC
The stopgate was located in a channel with dimensions of 3m wide by 5m deep. As with the MFEC penstock, the design was subject to independent FEA analysis and constructed of stainless steel. The stopgate was designed to fit within the channel’s existing rebates and isolate against a head of water equal to the full depth of the channel.
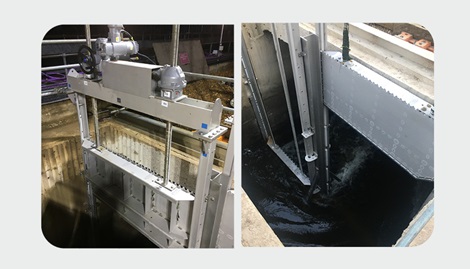
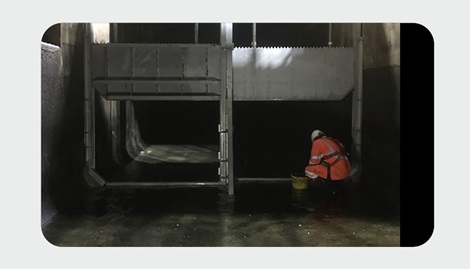
3 - Survey, condition report and emergency plan for Penstock 5.
An integral part of the enabling works to allow the scheme to go ahead involved closing an upstream penstock (Penstock 5). If this penstock was to seize once closed it would have led to the flooding of the Mogden works.
Glenfield Invicta undertook a condition survey of Penstock 5 for Thames Water and developed and implemented an emergency plan to lift the gate open should it seize shut. The system involved a frame and four hydraulic jacks that could be used to open the gate without the use of the actuator or need for an entry in the live channel. Thankfully, the system was not utilised, but Thames Water were nonetheless reassured by the peace of mind it provided.
4 - Inspection and refurbishment of the existing Bypass Culvert Isolation penstock (Penstock 6)
Thames Water’s initial plan was to replace Penstock 6, however, for operational and safety reasons, this was deemed to be impracticable.
Glenfield Invicta undertook an inspection of the penstock which turned out to be a cast iron Glenfield penstock installed during the construction of Mogden STW in 1934. The inspection identified that the penstock was in good condition given its age, but had seized. This was rectified during Glenfield Invicta’s refurbishment of the penstock. The scope of this refurbishment included the upgrade of the previously manually operated penstock through the retrofitting of a variable speed electric actuator and UPS system that automatically powers the penstock fully open on loss of mains supply.
Cast iron penstocks are prone to seizure, particularly if left closed for long periods of time. This is one of the many reasons that cast iron has now largely been superseded by stainless steel penstocks.
After refurbishment and servicing, however, Glenfield Invicta expects its 86-year old penstock to enjoy many more decades of service.
Alex Philo was Glenfield Invicta’s lead on the Mogden penstock project:
‘This was an exciting, diverse and high-profile project in one of the UK’s largest sewage treatment plants; meeting timescales whilst maintaining the highest quality at all times was critical. It was extremely rewarding to play an important part in implementing such an innovative solution to a significant environmental issue.
All of our penstock expertise and experience in bespoke design, working with antiquated assets, and confined space installation was truly put to test. That being said, we apply the same skills, attention to detail and commitment to all of our penstock projects, large or small.
The installation phase required some really detailed logistics planning as work could only proceed at night when effluent flow rates were low and there was also a low tide in the Thames. This aspect of the scheme definitely reinforced the value to the client and principal contractor of us having our own full-time specialist penstock installation team.’
If you would like to know more about this project, or advice on your penstock installation, please contact Alex Philo on the details above. Call him on the number shown or click the email icon to write to Alex directly.