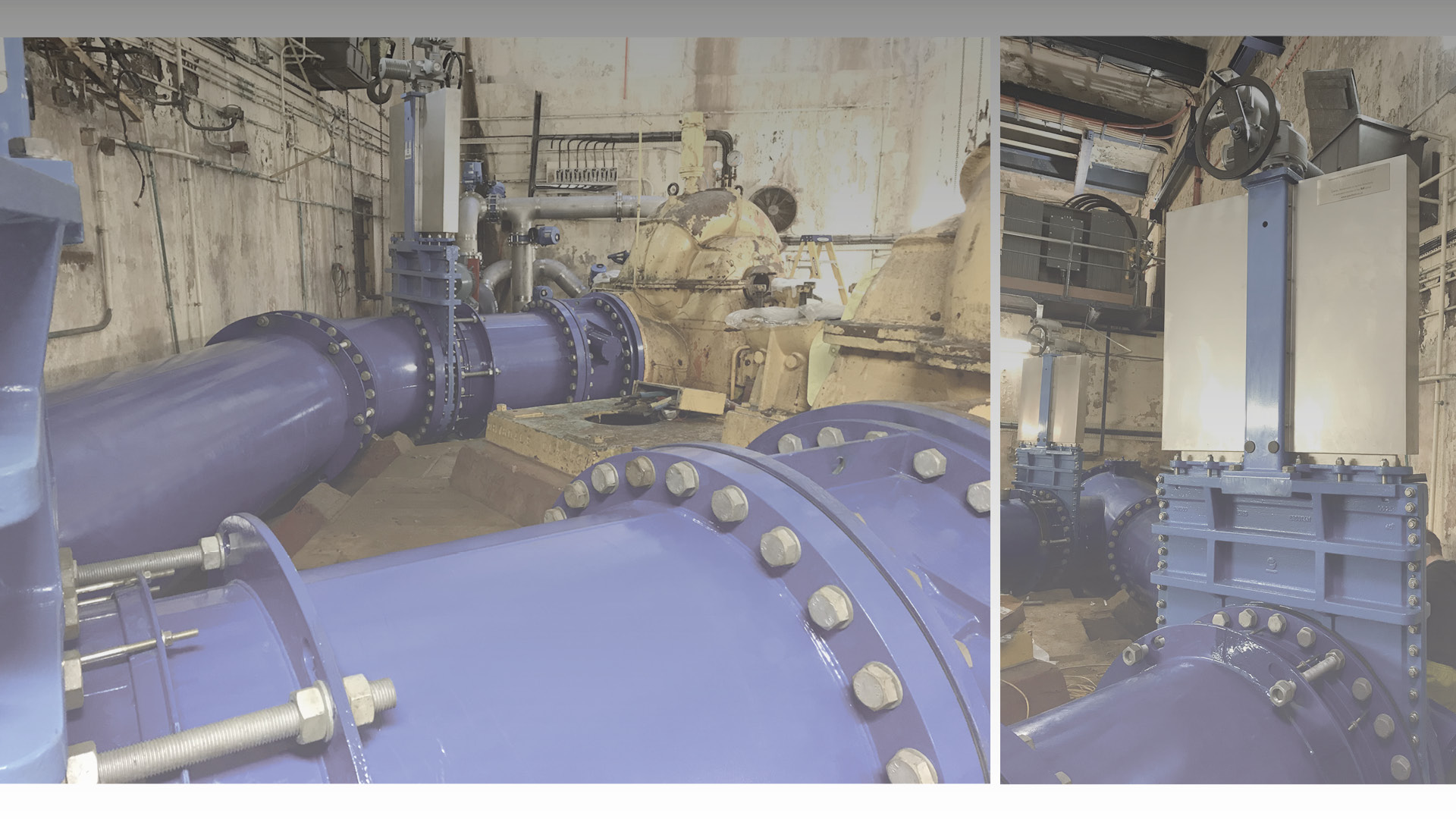
Refurbishment of Pump Discharge 8 Metres Below Ground
The River Clyde is synonymous with shipbuilding. It is estimated that the shipyards on the Clyde have collectively built 30,000 ships in the 175 years since Robert Napier built the first steamships there.
Today, the Clyde remains a centre of shipbuilding excellence and recently a significant sum of money has been invested in upgrading the facilities at 2 of the shipyards.
Valve Refurbishment Capability
The work was focussed on refurbishing the Dry Dock. Once completed, the refurbished dry dock – also referred to as a ‘graving dock’ – will provide the UK with the operational capacity to compete for ship refurbishment contracts in the global market.
Farrans is the main civils contractor and AVK’s involvement in the project started with a phone call back in May 2018, after the engineering team had been surveying the Dry Dock pumping station and had noticed the Glenfield name on the valves. Glenfield Invicta's Contract Manager, visited site to carry out a full audit. The valves and pipework were about ninety-five years old and had not been used for over half of that time. A collective decision was reached that the existing valves and cast iron pipework were beyond economical repair.
In September, Glenfield Invicta was awarded the contract to manage the refurbishment of the pump discharge. The project required the removal of the existing steelwork access platform, valves
and pipework and the supply and installation of a modern equivalent replacement.
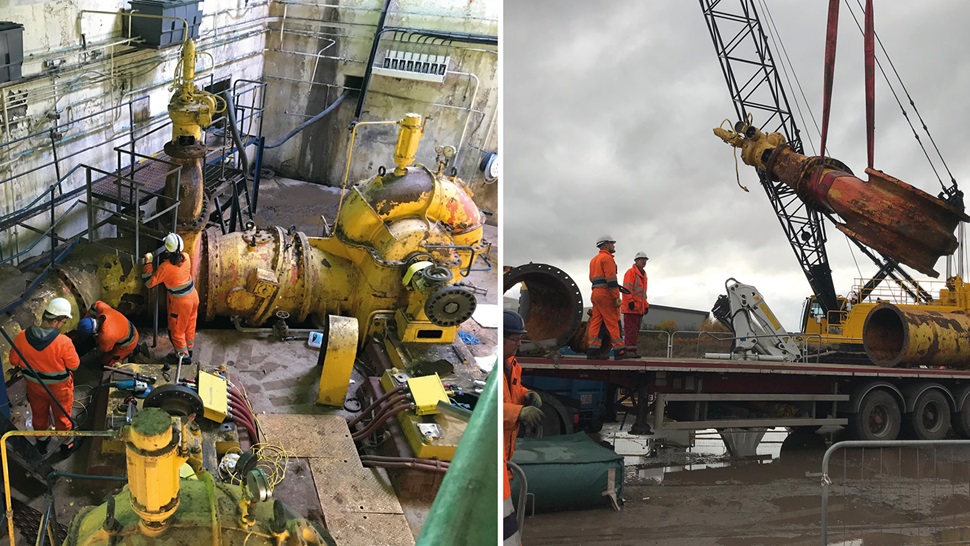

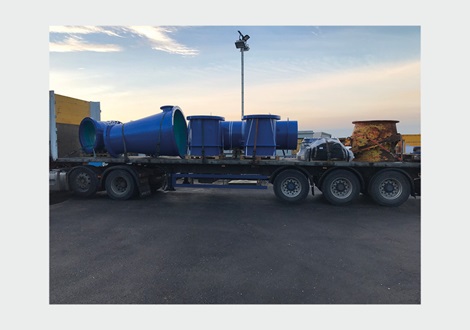
Knife Gate and Check Valve Suppliers
The replacement knife gate and check valves were sourced from Orbinox and ACMO respectively. Orbinox (Spain) and ACMO (Italy) are both AVK Group companies.
The exact specifications of the replacement valves were as follows:
- AVK Orbinox; DN1000, EB, actuated knife gate valve, PN16 (x2)
- AVK ACMO; DN1000 221SD, slanted seat, tilting disc check valve PN16 (x2).
The logistics of the project were far from straightforward. The pumping station is 8m below ground, in line with the base of the dock. This is common practice with dry docks as it optimises pump efficiency. Once a ship is in place and the dry dock gates are closed the water is pumped out and returned to the Clyde at low tide.
Entry to the pumping station is via a 2.6m² access hatch at ground level. All materials had to leave and enter the pumping station via the hatch. The pipework reached DN1500 diameter at one point so great care was needed to ensure the work was completed without damage, both to the structure and to the live 11kV power cable located very close to the hatch. A further complication was that no welding was allowed on site and burning gear could not be used.
The site work was undertaken by a team of six service engineers from Invicta Valves, an AVK Group company. The engineers came from Invicta’s headquarters in Maidstone and from its branch in Kilmarnock. Site Health & Safety and security were extremely important and all Glenfield and Invicta personnel had to undergo a strict vetting process, in addition to completing confined spaces training, an emergency response team was also located on site at all times.
After the cast iron pipework was removed from site it was reassembled and detailed dimensional measurements were made to create a template.
A duplicate carbon steel pipework system was then fabricated in sections. Many of the pipework fittings were bespoke including a DN1500 to DN1000 reducing tee and a 40° bend.
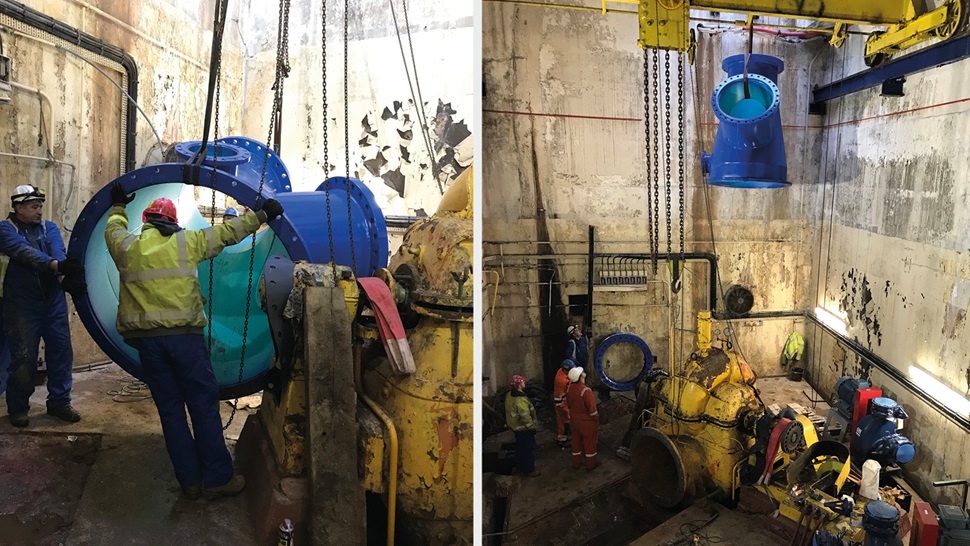
‘Glenfield secured the work and our team of specialist engineers proved invaluable throughout. Before the project reached site, we effectively switched to Invicta, with GlenfieldPaul Boyden - Director, AVK UK Water Projects
acting as the Contract Manager, responsible for project delivery alongside the Invicta site engineers. The support received from our sister companies, Orbinox in Spain and ACMO in
Italy was excellent and contributed to a really effective project delivered on time and to budget. Rebuilding the pump discharge system with only minor site adjustments was a testament to the professionalism of the AVK team.’