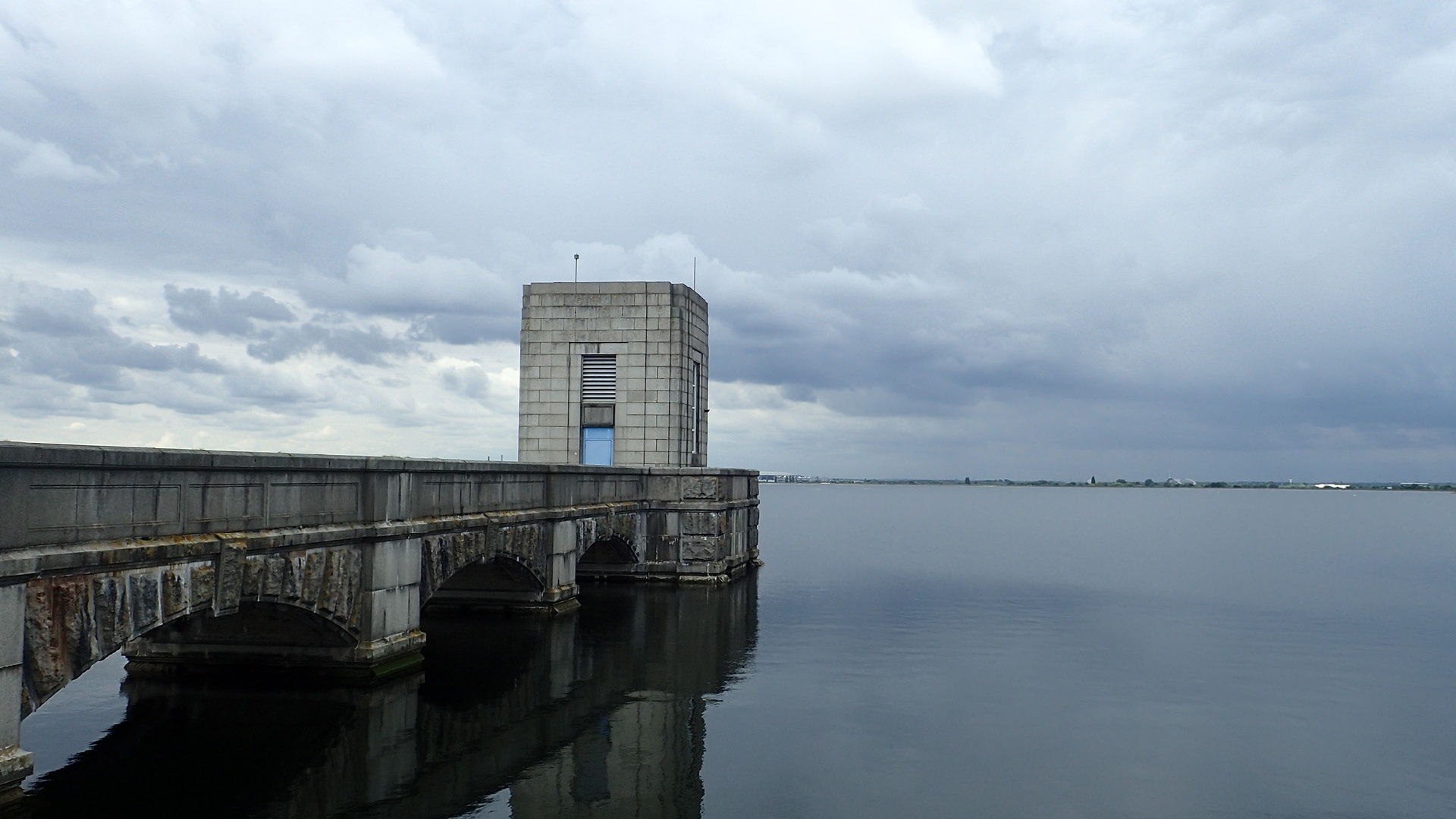
Collaborating to replace and refurbish critical valves
Background Info
The King George VI reservoir is owned and managed by Thames Water. Located close to Heathrow Airport, it is integral to the supply of clean drinking water to those living in West London.
The Challenge
The outlet valve tower, located in the south of the reservoir, houses eight valves at four draw-off levels. The valves are the original 48” wedge gate valves which have been in place for over seventy years. The challenge was to refurbish the top draw-off valves and return the reservoir to a fully operational state to allow water to be drawn off from the top level.
Valves seized in the closed position
Thames Water engineers identified that both of the top draw-off valves had seized in the closed position; the valve spindles were rotating but there was no linear movement of the valve gates. A camera survey was carried out at the time to determine the root cause of the failure. This survey clearly showed that the threads had been ‘stripped’ from both the spindles and the nuts.
The valves were designed to be manually opened and closed, and later were retro-fitted with an actuator and gearbox arrangement. This arrangement, combined with other gearing on the valve, appears, over time, to have contributed to excessively high operating torques for valves of this design.
Glenfield Invicta brought in by Barhale
Civil engineering contractor Barhale brought in Glenfield Invicta to design and deliver a solution that would return the valves to full working order. Barhale’s undertook the civils and lifting operations, whilst Glenfield Invicta was tasked with project managing the valve repair works.
The King George VI project is typical of many where Glenfield Invicta’s knowledge and experience has been called upon to resolve complex engineering challenges. On some projects this has involved Glenfield Invicta working independently and on others, as here, as part of a multi-disciplinary team.
Collaborative working
A key factor in delivering a successful outcome was the collaborative working relationships built across the Glenfield Invicta, Barhale and Thames Water teams. Ken Ottley was Glenfield Invicta’s lead engineer on the project.
The Solution
The design of the tower meant that removing the spindles for detailed investigation and replacement would be challenging; the spindles were almost 2.5m (96”) long and 11.5cm (4.5”) in diameter. The fact that several other contractors were reluctant to tender for the works is witness to the degree of challenge involved.
Glenfield Invicta preparing to refurbish valves and spindle at King George VI reservoir.
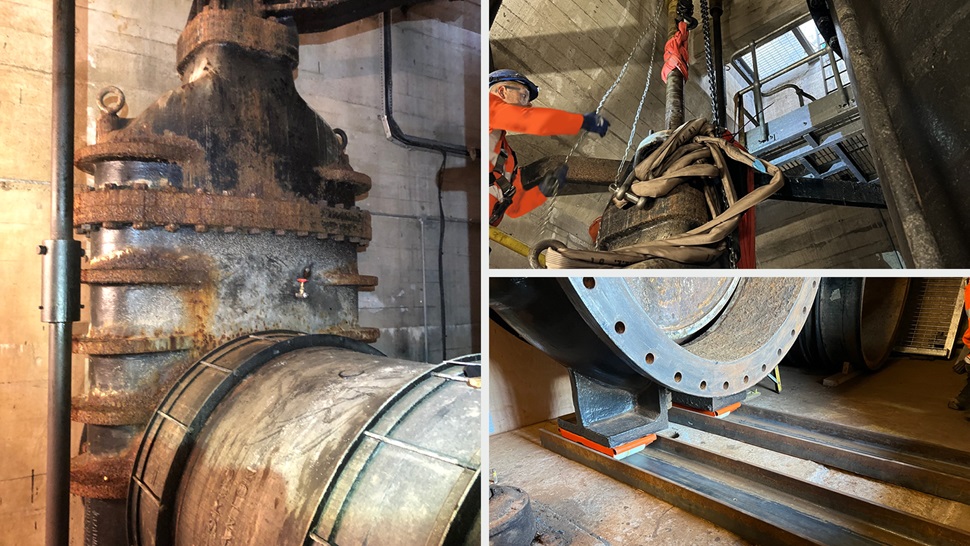
Sequencing
A detailed programme of works was developed and agreed, with close attention paid, in particular, to the sequencing of the many steps required to remove, and reinstall the spindles. These steps would require complex enabling and lifting works alongside heavy mechanical engineering in a confined space. Unsurprisingly, the programme submitted incorporated comprehensive risk assessments and detailed method statements supported by high-level safe systems of work.
Moving the valves
The gates were released from the valve bodies using the jacking screw located underneath each valve. The next step was facilitating the removal of the valve spindles along with the nuts so they could be lifted up and out of the tower for further investigation and replacement. As mentioned earlier, the valve spindles were almost 2.5m long. A clearance height of some 3m between the top of the valve and the chamber would be required. Unfortunately, the ceiling design above the valve tapered inwards in a corbel design meaning that the valves, each weighing 5 tonnes, would have to be moved towards the centre of the tower’s shaft to provide sufficient clearance.
Conventional crane lifting was not possible as the floor above the valve was made of solid concrete supporting all of Thames Water’s valve actuators and telemetry. Furthermore, there was no existing structural supports that could be used to lift the valves.
Lifting plan
The lifting plan developed by Barhale used a combination of chain blocks, slings and shackles, supported by a 5 tonne-rated I-beam spanning the space above the valves; the beam was proof-tested prior to use. Existing core holes allowed the slings and chains to pass from one floor to the next.
To achieve a plumb lift from the top of the valve, the line of the chain block was braced using lifting slings (see images). The slings were attached to the wall of the tower using chemical anchors, threaded bar and lifting eye nuts. Once the lifting mechanism was in place, the valves were carefully lifted by 15cm. This clearance was sufficient to allow the valves to be transferred to a ‘rail and skates’ mechanism. This mechanism was used to gradually ‘pull’ the valves towards the centre of the chamber (see images).
Dismantling the valves and removing the spindles
Glenfield Invicta developed a detailed sequencing plan for the dismantling of the valves. Detailed RAMS were prepared including a sketch showing the required gate position to allow for the nut to be removed.
The valves were dismantled, allowing for abstraction of the spindles. This operation meant the spindles could be carefully lifted up and out of the valve tower shaft. The bearings and nuts were removed by Glenfield Invicta for cleaning, inspection and regreasing.
Reverse engineering
Inspection of the spindles showed sections of the screw’s thread were completely stripped. Consequently, two new spindles were reverse engineered using enhanced materials. The length of the spindles limited the number of suppliers in the UK with a long enough lathe bed to machine them. New nuts were also machined using drawings prepared by Glenfield Invicta.
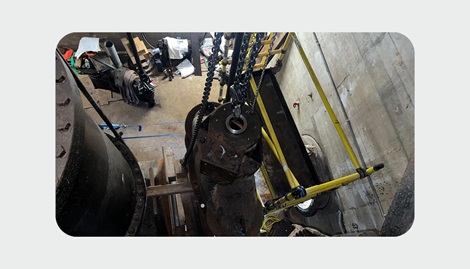
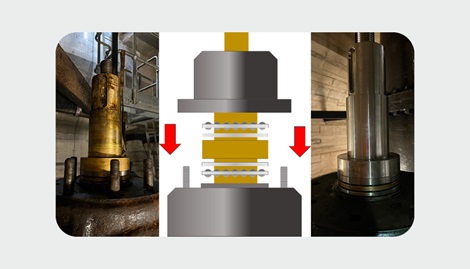
Rebuilding and recommissioning
The new spindles were delivered to site. They were carefully wrapped in protective material to minimise the risk of damage as they were lifted by the Barhale team back down the shaft and into the chamber. The valves were rebuilt to accommodate the new spindles and then moved back into position using the lifting apparatus detailed earlier in this case study. The actuator operating settings were optimised and the valves commissioned. The works were successfully signed off just before Christmas 2022.
Glenfield Invicta replace the refurbished valves and spindle at King George VI reservoir
A very challenging project
Bryn Philpott, Senior Reservoir Engineer, was Thames Water’s Supervising Engineer on the project:
‘This was one of the most challenging projects I have been involved with, particularly from an access and lifting perspective. Its success was due in no small part to the collaborative approach adopted by all those involved in its implementation. When the refurbished valves were tested, I had never heard valves operating so quietly.’
Steve Best, is a Senior Project Manager with Barhale:
‘This was a particularly challenging piece of work that, to our knowledge, has not been done before under similar circumstances.
The collaboration between the Barhale and Glenfield Invicta teams to bring together our different areas of expertise was essential for success. This collaboration led to a “one team” approach on site, with everyone working together to the same goal and delivering a very successful project.’
Ken Ottley, Glenfield Invicta’s lead engineer on the project, has been tasked with completing a detailed investigation of the spindles, valves and actuators to determine possible failure modes:
‘I am grateful for having had the opportunity to work on such an interesting and demanding project, and proud to have successfully completed it. When I work on projects like King George VI Reservoir, I am aware that I am building on Glenfield Invicta’s 170 years of engineering heritage. I made some great friends on site which made the project even more rewarding. There is a huge desire to maintain the goodwill we have built and work together again on future projects.’
Contact Ken Ottley to discuss your project requirements on the details above - call or or click on the email icon to write to Ken directly.